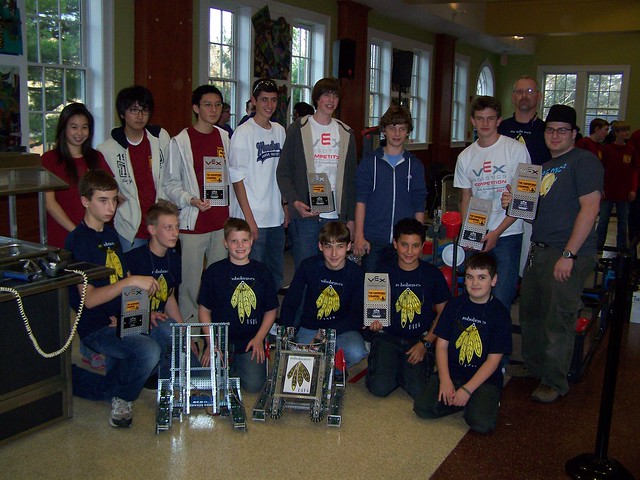
So, last I posted in the VRC1414 blog Casey, Mitch, Bryan, Jonas, Justin, and Ben were all prepared for our first event in November. As reported via facebook and twitter, our rookie team performed very well for the first time out at the Haverford Stampede on Nov 19. We were the number two overall seed losing only one qualifying match, were event champs with 3057, and 169B as alliance partners, and also won the Build Award. All six team members were very good in their roles the first time out for sure! Below is a photo at the conclusion of the event together with our partners and the rest of the photos from the day can be seen here:
http://www.flickr.com/photos/uprobotics/sets/72157628058398433/
Even though our performance exceeded expectations, we certainly were able to identify places we could improve. So, during a nice break from meetings all the way through the new year we compiled our list for improvement via email, video review, etc to plan our next steps. That list included:
1. Improve ground speed by swapping the 2.5" omni wheels for 4" omni wheels. We were defended pretty heavily once we proved to be a consistent scorer and feel the approximately 40% improvement in ground speed to go along with our agility could help up be more a proficient scorer in the future,
2. Tighter motor fastening by swapping out all motor screws for screws with thread locker. While we like a busy pit crew, we were tightening motor screws way too much at the Stampede.
3. Exchange our eight "spliced" threaded beams in our drive modules for single 2.5" beams. Dealing with the "extra parts" nearly cost us making match time once when we had to make a pre-match adjustment and this easy switch out is a no-brainer.
4. Improve control over our arm and robot position in autonomous as well as adding selectable options for autonomous sub-routines through use of sensors. Although we performed well in autonomous at the Stampede, we were entirely dependent upon human positioning of the robot and battery voltage - which led to a few misses we'd rather eliminate.
From that list we ordered some additional parts, took some needed time with family for the holidays, toured the team trophies around to everyone's house, the head coach did some sensor/programming learning, and we added three January meetings and one Feb meeting to our schedule to prepare for our next event on Feb 18.
So, thus far we've had two of our Jan meetings and Kwelaha 1.5 is coming along with improvements.
1. All motor screws, threaded beams, and wheels are switched out. This proved to be more tedious than we had planned as a few of the motor screws were really difficult to place (but we got em!) and the new wheels elevated our robot 3/4" and messed up our intake geometry - jamming barrels way too frequently. So after several iterations and tests at and between meetings (thanks to Jake who will be joining VRC1414 in the spring for the extra help) we settled on moving our chassis cross members that serve as a hard stop for the accumulator one hole toward the rear of the robot to grab the barrels a little lower and just before today's meeting ended (thanks for the idea, Mitch!) we swapped out 2.5" threaded beams for 3" threaded beams that support the top of our polycarbonate sandwich to improve clearance.
2. Sensors are mounted (4 bumper switches and one quad encoder) along with a new length of shaft we cut to accommodate the encoder. Test programming for the bumper switches shows promise, the encoder still needs some work. Stay tuned for next week's update on our autonomous improvements when we'll give detail to our plan.
3. We spent about an hour doing 2:00 at a time driver practice with varied drive teams today to get a good feel for our improved robot mechanically. We're on our way to learning how to handle our changes and I'm excited by the quick progress after the long layoff in addition to having a faster machine.
Photos from our Jan meetings (thus far) are here:
http://www.flickr.com/photos/uprobotics/sets/72157628904216381/
Looking forward to our two remaining meetings and the Feb event!